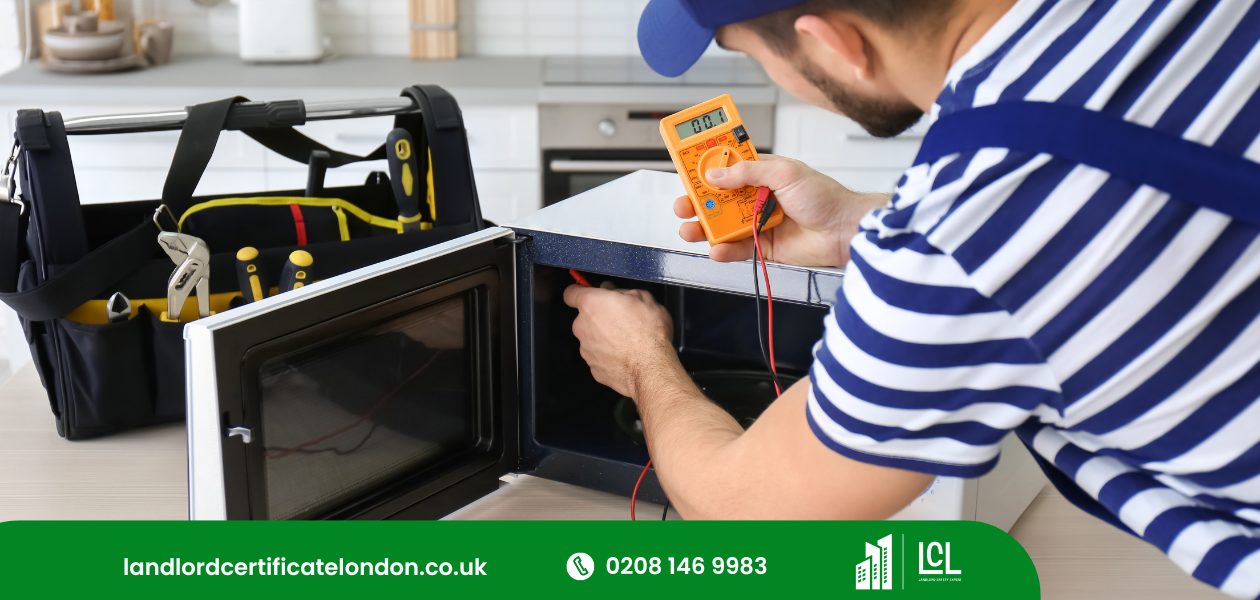
The Portable Appliance Test (PAT) procedure is an essential safety protocol that scrutinizes electrical portable appliances to ascertain their operational safety. This process involves meticulous visual inspections to detect any signs of wear or damage and includes a series of stringent electrical tests tailored to the specific class of the appliance. By adhering to this procedure, organizations can significantly mitigate the risk of electrical accidents, ensuring a safer working environment. However, the intricacies of the tests and the implications they hold for both safety compliance and operational continuity raise several critical considerations. What are the underlying standards governing these procedures, and how do they impact the interpretation of test results, Let’s understand What Is a Portable Appliance Test Procedure?
what is PAT Testing & What Is a Portable Appliance Test Procedure?
Portable Appliance Testing (PAT) is a critical examination process used to verify portable electrical devices’ electrical safety and operational integrity in various settings, including workplaces and residential areas.
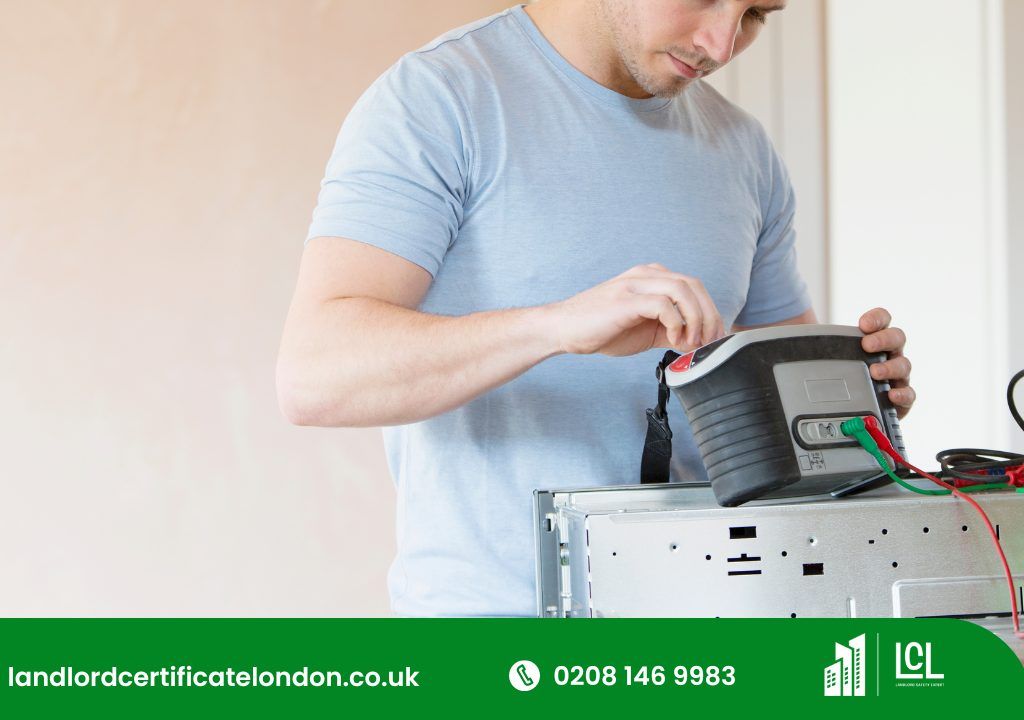
What Is a Portable Appliance Test Procedure?
Originating in the UK during the early 1960s, PAT testing began primarily in government estates, aimed at preventing electrical accidents in increasingly technologically equipped offices. Over time, this practice expanded across various sectors, underscoring the necessity for regular electrical safety checks to mitigate hazards associated with using portable electrical equipment.
Despite its established history, several misconceptions persist about PAT testing. Commonly, there is a misunderstanding that it is a statutory requirement enforced by specific laws; however, it is not explicitly mandated by legislation.
Instead, the Electricity at Work Regulations 1989 require that electrical equipment must be maintained to prevent danger, not specifically that it must undergo PAT testing. This has led to the misbelief that PAT testing is legally obligatory, whereas it remains a highly recommended best practice.
Employers often adopt PAT testing as a proactive measure to ensure compliance with broader health and safety obligations, thereby fostering safer working environments.
Importance of PAT Testing
While PAT testing is not mandated by law, its significance in ensuring electrical safety cannot be overstated. This testing procedure serves as a fundamental component in the broader field of risk management within workplace environments. It systematically evaluates the operational integrity of portable electrical appliances, mitigating potential hazards that could lead to serious injuries or costly damages.
Here are key reasons emphasizing the importance of PAT testing:
- Prevention of Electrical Accidents: Regular testing identifies defects that may lead to electrical fires or electrocution, significantly reducing the occurrence of such accidents.
- Compliance with Safety Regulations: Although not legally required, PAT testing supports compliance with the Electricity at Work Regulations 1989, which demand that all electrical systems be maintained to prevent danger.
- Enhanced Equipment Longevity: By detecting and rectifying faults early, PAT testing extends the usable life of electrical appliances, ensuring they operate efficiently and safely over time.
The process of PAT testing integrates seamlessly into an organization’s safety protocols, reinforcing a culture of safety and responsibility.
PAT Testing Process
The process of PAT testing begins with a thorough visual inspection of the appliance to identify any obvious signs of damage or wear that could affect its safety. This initial assessment is critical as it can pinpoint issues that might not be detected during later testing stages.
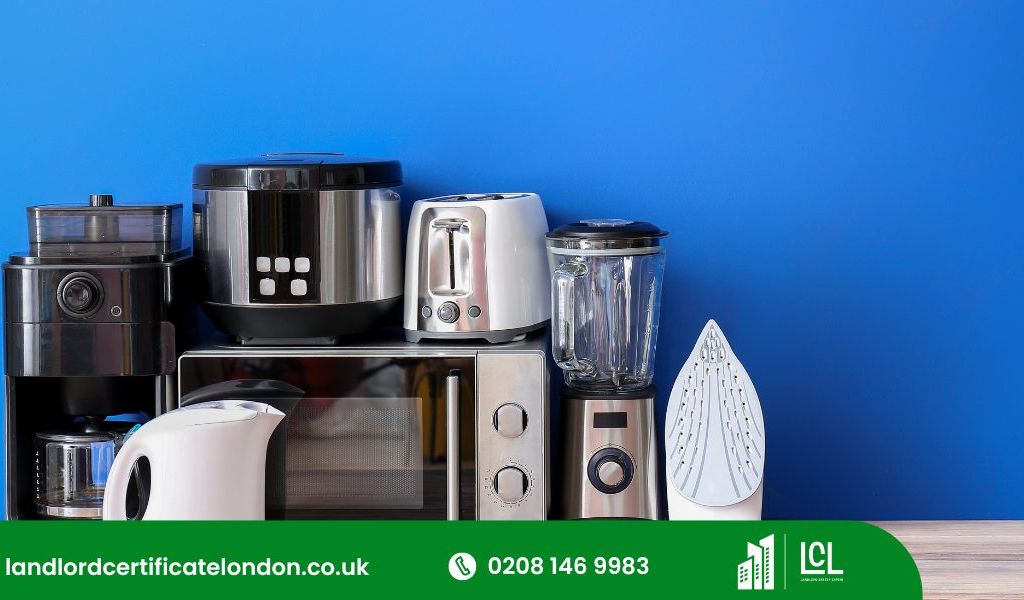
After this, the specific test equipment is employed depending on the class of the appliance and its general condition. The test equipment used is designed to meticulously adhere to established testing standards, ensuring each appliance is evaluated under uniform criteria.
For Class 1 appliances, tests like Earth continuity and insulation resistance are conducted. Class 2 appliances undergo similar insulation tests but without Earth continuity due to their double insulation design. Each test aims to confirm the integrity and safety of the appliance’s electrical systems and components.
Throughout the testing process, detailed records are maintained for each appliance. These records include the condition of the appliance, the tests performed, the results obtained, and any recommendations for repairs or adjustments.
This documentation is essential for tracking the appliance’s safety status over time and ensuring compliance with safety regulations. The precision of the testing process, coupled with stringent adherence to testing standards, guarantees a high level of reliability and safety in appliance usage.
Frequency and Requirements
Determining the frequency of PAT testing and establishing requirements is guided primarily by the type of appliance, its usage, and the environment in which it operates. The overarching goal is to ensure that all portable electrical appliances are maintained in a safe and functional state, thus mitigating any risks associated with their operation.
To effectively manage PAT testing intervals and appliance maintenance, consider the following:
- Assess Usage Frequency: Appliances used daily may require more frequent testing than those used infrequently. High-demand environments exacerbate wear and tear, necessitating closer monitoring.
- Evaluate Environmental Conditions: Appliances operating in harsh conditions, such as excessive moisture, heat, or dust, are at a higher risk of degradation and should be tested more regularly.
- Compliance with Regulatory Standards: Adherence to local safety regulations and standards is essential. These may dictate minimum testing frequencies for specific types of appliances or environments, ensuring that all potential hazards are systematically addressed.
Classes of Appliances
Understanding the classes of appliances is fundamental to establishing effective PAT testing protocols. In the realm of portable appliances, categorization into Class 1, Class 2, and Class 3 is pivotal for conducting precise risk assessments and ensuring safety.
Class 1 appliances, including heavy machinery and desktop computers, are identified as high-risk due to their reliance on earthing and robust insulation. Such appliances necessitate comprehensive testing to verify earth continuity and insulation integrity.
Class 2 appliances, like hairdryers and power tools, present a moderate risk. These are double insulated, reducing the need for earthing, but still require thorough insulation checks to prevent electrical shock.
Class 3 appliances, which include low-voltage devices such as chargers and cameras, pose the lowest risk. Typically, these require minimal testing, often limited to visual inspections, due to their inherent safety features and lower voltages.
The differentiation of appliance categories aids technicians and safety managers in prioritizing testing efforts and allocating resources efficiently. Understanding these classifications enhances the precision of risk assessments, directing focus toward appliances that pose significant hazards, thereby optimizing safety protocols and maintaining compliance with health and safety standards.
Testing Methods
How do technicians ensure the safety and efficiency of electrical appliances? The answer lies in adhering to stringent Portable Appliance Testing (PAT) methods which incorporate the use of specialized testing equipment and compliance with established testing standards. These procedures are critical in minimizing electrical hazards and ensuring appliance functionality.
Here are the core aspects of the testing methods used in PAT:
- Visual Examination: Before any electrical tests are conducted, a thorough visual inspection is performed to check for any signs of damage, wear, or incorrect configuration that could pose safety risks.
- Earth Continuity Test: This test is crucial for Class 1 appliances. It involves measuring the resistance of the earth’s continuity path using a low-voltage test current. This ensures that there is a safe path for the fault current to travel to the ground, which is essential for preventing electric shocks.
- Insulation Resistance Test: This test is conducted on all classes of appliances to assess the quality of insulation between the current carrying parts and any exposed metal that could become life. High insulation resistance is a good indicator that the appliance is safe to use.
Training and Resources
To ensure the effectiveness and safety of PAT testing, a robust training program and access to comprehensive resources are essential. Professionals engaged in PAT testing must undergo specialized training workshops that cover theoretical knowledge, practical skills, and the latest industry standards. These sessions should include hands-on experience with various classes of electrical appliances and familiarization with both common and complex issues that might arise during testing.
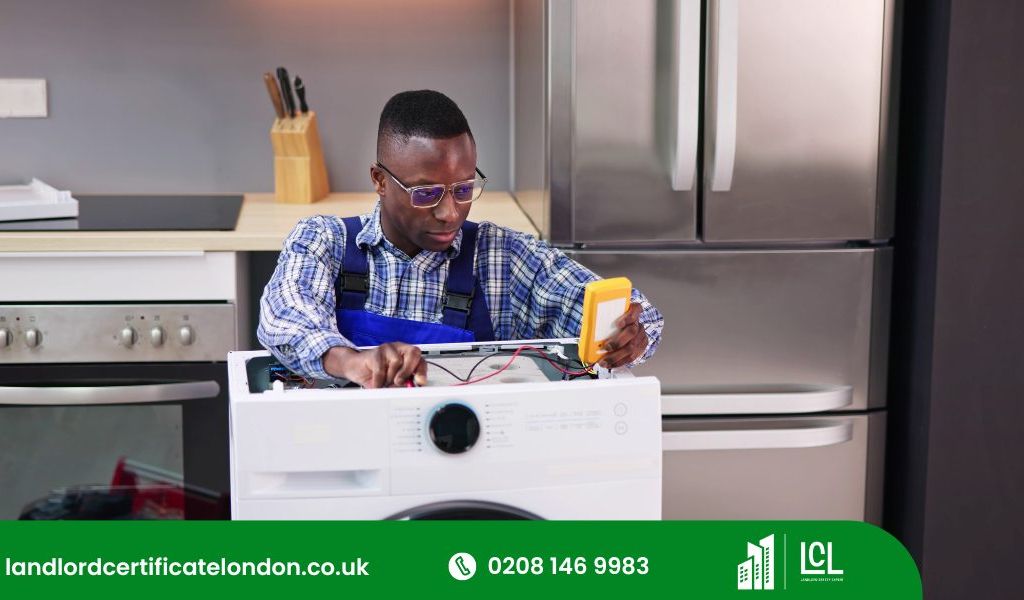
Moreover, online resources play a crucial role in the continuous education of PAT testers. Advanced online platforms offer modules that detail step-by-step procedures, case studies, and updates on regulatory changes. These resources are invaluable for ensuring that testers remain abreast of new technologies and testing methodologies. They also provide forums for testers to exchange insights and solutions, thereby fostering a community of knowledgeable professionals dedicated to maintaining high safety standards.
Access to detailed manuals, instructional videos, and real-time support systems further enhances the training experience, ensuring that PAT testers are well-equipped to perform their duties proficiently.
Safety and Compliance
Building on the foundation of thorough training and extensive resources, safety, and compliance in PAT testing represent the core objectives that guide the effective application of these practices. Ensuring the electrical safety of portable appliances not only mitigates risks but also aligns with regulatory standards, safeguarding both people and property.
In the realm of risk management, PAT testing is pivotal for:
- Identifying Potential Hazards: Early detection of electrical defects prevents accidents and enhances workplace safety.
- Ensuring Compliance: Regular PAT testing ensures adherence to the Electricity at Work Regulations 1989, which mandate the maintenance of electrical systems to prevent danger.
- Documenting Safety Protocols: Detailed records from PAT tests provide a traceable accountability framework that supports compliance and continuous improvement initiatives.
Each phase of the PAT procedure is designed with precision to dissect and evaluate the safety status of electrical appliances meticulously. This not only fosters a culture of safety but also instills confidence among stakeholders about the operational integrity of their electrical assets.
Thus, PAT testing is an indispensable tool in the arsenal of an organization’s safety and compliance strategy.
Conclusion
In conclusion, Portable Appliance Testing (PAT) embodies a critical protocol aimed at safeguarding electrical safety across various settings. This methodical approach not only helps in identifying potential hazards through visual and electrical examinations but also ensures compliance with rigorous safety standards. By categorizing appliances and applying appropriate testing procedures, PAT serves as an indispensable tool in mitigating electrical risks, thereby enhancing overall safety. Regular updates in training and adherence to defined frequencies further bolster the effectiveness of this preventive measure.
About the Author: LandlordCertificate
Related Posts
Get Social
Recent Posts
- Cost of EICR Certificate: Prices, Factors, and Essential Information
- Steps of Fire Risk Assessment: How to Protect Your Property and People
- Fire Safety Certificate for Flats: A Complete Guide for Landlords & Residents
- CP42 Gas Certificate: The Essential Commercial Gas Safety Certification
- Fire Alarm LD3 / A Complete Guide to Category LD3 Fire Safety Systems