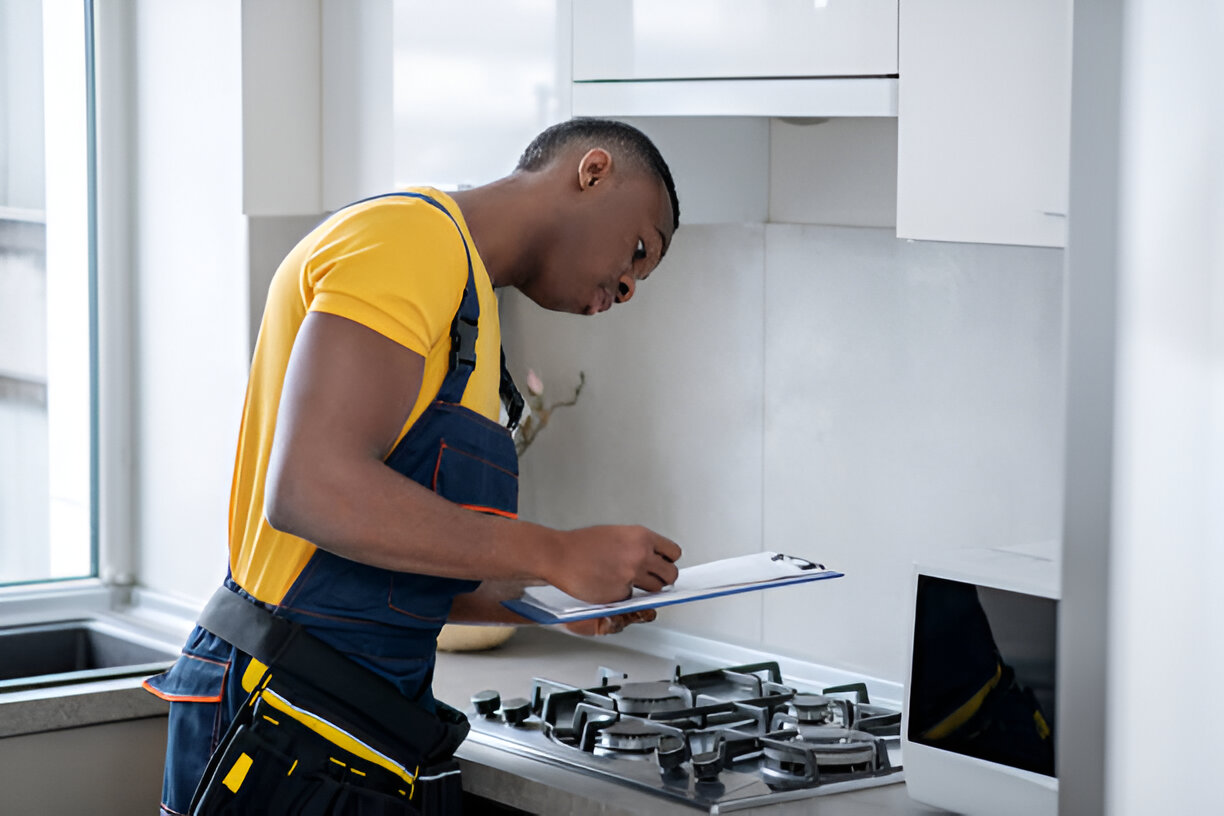
In the realm of new construction, the issuance of a Gas Safety Certificate stands as a critical checkpoint that underscores not only compliance with stringent legal standards but also a commitment to occupant safety. As developers and builders navigate the complexities of ensuring that all gas installations meet the required safety protocols, this certification emerges as a pivotal marker of reliability and quality in building projects. However, the process of obtaining this certificate entails a series of meticulous steps and checks, which raises pertinent questions about the challenges and intricacies involved. What are the common pitfalls, and how can they be effectively mitigated to streamline certification, Let’s understand Gas Safety Certificate for New Builds.
Importance of Gas Safety Certificates
A Gas Safety Certificate serves as a crucial safeguard for homeowners, ensuring that all gas appliances, fittings, and flues are installed correctly and operate safely.
This certification is pivotal not only for maintaining safety standards but also for enhancing the integrity of a building’s infrastructure.
For new builds, where installation errors are possible and potentially catastrophic, the certification assures that gas systems meet rigorous safety criteria.
It protects against the risks of gas leaks, which can lead to fire hazards or carbon monoxide poisoning.
Furthermore, the certificate is an essential tool for builders and engineers seeking to affirm the quality and dependability of their work, serving as a benchmark for professionalism and adherence to best practices in construction.
Legal Requirements for Certification
Building on the foundational importance of Gas Safety Certificates, it is imperative to understand the legal requirements surrounding their issuance for new constructions.
The legislation mandates that all new buildings with gas installations receive this certification before they are deemed habitable. This requirement ensures that all gas works comply with national safety standards, aiming to prevent hazards such as gas leaks or explosions.
Compliance is monitored by relevant governmental bodies, which stipulate that the certification must be obtained prior to occupation. The legal framework is designed not only to protect residents but also to maintain public safety and confidence in gas systems.
Failure to secure a Gas Safety Certificate can result in legal sanctions, including fines and restrictions on building use.
Qualified Professionals for Inspection
To ensure the integrity of new gas installations, only qualified professionals are authorized to conduct the mandatory inspections required for Gas Safety Certificates.
These individuals must possess specific qualifications and be registered with an accredited body, such as the Gas Safe Register in the United Kingdom. This certification ensures that the inspector has undergone rigorous training and assessments related to gas safety and compliance.
Their expertise enables them to precisely evaluate the installation’s adherence to current safety standards and regulations.
Furthermore, their evaluations play a crucial role in preempting potential hazards associated with gas systems. Engaging such professionals not only fulfills legal obligations but also secures the safety and efficacy of the building’s gas supply system.
Steps to Obtain a Certificate
To secure a Gas Safety Certificate for a new building, the property owner must initially contact a registered and qualified inspector. Following this, the process involves a series of systematic steps designed to ensure the safety and compliance of the gas installations within the property.
- Documentation Preparation: Gather all necessary construction and installation documents about the gas systems for review.
- Inspection Appointment: Agree on a suitable time for the inspection, ensuring that the site is accessible and all gas systems are operational.
- Rectifying Issues: After the inspection, address any identified issues promptly. Compliance with safety standards is crucial for certification.
Adhering to these steps meticulously will facilitate a smooth certification process, enhancing safety and regulatory compliance.
Timing and Scheduling Inspections
When scheduling inspections for a Gas Safety Certificate in new builds, timing plays a critical role in maintaining project timelines and ensuring regulatory compliance.
Strategic planning of these inspections should align with key construction milestones to avoid delays. Typically, the initial inspection should be integrated after the installation of gas lines and before interior finishing begins. This allows for any necessary adjustments or corrections early in the process.
Scheduling should consider the availability of certified inspectors and potential lead times for booking, which can vary greatly depending on regional demand.
To streamline the process, developers should establish regular communication channels with inspection bodies and possibly integrate automated scheduling systems. This proactive approach will facilitate timely approvals and contribute to the seamless progression of construction projects.
Common Inspection Failures
In addressing common inspection failures, it is essential to identify and understand the typical issues that can impede the issuance of a Gas Safety Certificate in new builds.
By pinpointing these problems early, constructors and developers can take preemptive steps to ensure compliance and safety standards are met.
- Improper Ventilation: Insufficient ventilation can lead to dangerous gas build-ups, which are a critical safety risk.
- Faulty Appliance Installation: Incorrectly installed gas appliances may lead to leaks or inefficient operations, both of which pose significant hazards.
- Non-compliant Gas Piping: Using substandard materials or incorrect piping sizes can result in non-compliance, potentially leading to leaks and pressure discrepancies.
These pitfalls highlight the importance of meticulous attention to installation and material standards in securing a Gas Safety Certificate.
Addressing Failed Inspections
Once a Gas Safety Certificate inspection fails, it is crucial for developers to act swiftly and efficiently to rectify identified issues. Immediate action not only ensures compliance but also reinforces the commitment to safety and quality in new builds. Addressing these concerns systematically can prevent future failures and associated delays.
Action Item | Benefit |
---|---|
Review Inspection Report | Identifies specific non-compliance areas |
Implement Corrections | Ensures alignment with safety standards |
Schedule Re-inspection | Confirms resolution of previous issues |
Developers should use the inspection report as a roadmap for corrective measures, ensuring that all faults are adequately addressed before the re-inspection. This structured approach prevents oversight and enhances the integrity of the building project.
Benefits of Compliance
Achieving compliance with gas safety standards in new builds offers tangible benefits that extend beyond merely meeting legal requirements.
Compliance ensures:
- Enhanced Safety: Rigorous adherence to regulations minimizes risks of gas leaks and potential fire hazards, safeguarding residents and property.
- Increased Property Value: Properties with up-to-date gas safety certifications are more attractive to potential buyers and renters, reflecting a commitment to safety and quality.
- Long-term Cost Savings: Identifying and rectifying potential gas safety issues during the initial building phase helps avoid costly repairs and legal complications in the future.
Maintaining Gas Safety Post-Certification
Securing a gas safety certificate is just the initial step in ensuring long-term safety and compliance in new builds.
To maintain this standard, regular audits and inspections are essential. Property managers should schedule annual checks with certified professionals to examine gas lines, appliances, and ventilation systems. This proactive approach not only adheres to legal requirements but also identifies potential hazards before they escalate.
Additionally, investing in training for occupants on the safe operation of gas appliances enhances safety awareness and reduces risk.
It’s crucial to establish a direct line of communication with gas safety experts, enabling swift responses to gas-related incidents.
Adherence to these practices ensures the enduring integrity and safety of the building’s gas infrastructure.
Our Pricing
Our Gas Safety Certificate Prices |
---|
Gas Safety Certificate 1 Appliance £45 |
Gas Safety Certificate 2 Appliance £55 |
Gas Safety Certificate 3 Appliance £65 |
Gas Safety Certificate & Boiler Service £74.99 |
Check Out Our Other Services
About the Author: LandlordCertificate
Related Posts
Get Social
Recent Posts
- Cost of EICR Certificate: Prices, Factors, and Essential Information
- Steps of Fire Risk Assessment: How to Protect Your Property and People
- Fire Safety Certificate for Flats: A Complete Guide for Landlords & Residents
- CP42 Gas Certificate: The Essential Commercial Gas Safety Certification
- Fire Alarm LD3 / A Complete Guide to Category LD3 Fire Safety Systems